Lean Six Sigma Green Belt Training
Step up to the second level of formal training in the world of Lean Six Sigma with our certified Green Belt program. This certification isn’t just globally recognized; it’s your golden ticket to mastering the art of process improvement. With guidance from seasoned Lean Six Sigma Black Belt professionals, you’ll not only learn the tools and methods but dive deep into the ‘why’ behind Lean Six Sigma. Get ready to take your Lean Six Sigma journey to exhilarating new depths, where theory meets practical mastery.
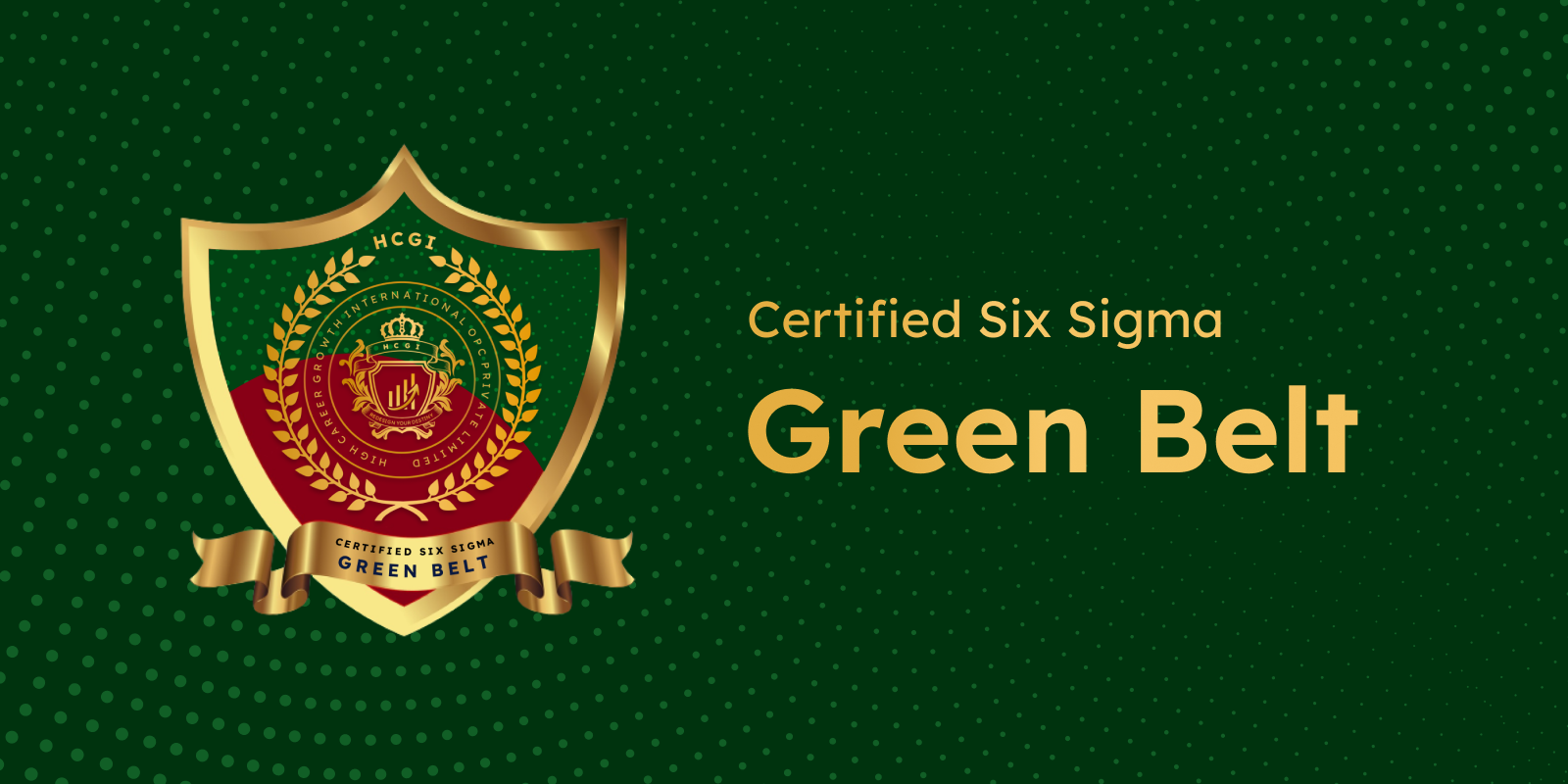
Key Takeaways
Key learning points for the Six Sigma Green Belt program at High Career Growth International, organized into four sections.
- Advanced Methodology and Project Management: In the Methodology and Project Management, you’ll delve into the DMAIC framework, gaining a deeper understanding of its principles. Additionally, you’ll acquire essential project management skills to effectively plan, execute, and oversee Six Sigma projects.
- Statistical Analysis and Process Optimization: In this approach, you’ll gain proficiency in advanced statistical analysis techniques, providing you with a robust data-driven decision-making toolkit. Moreover, you’ll master the art of process optimization, discovering methods to enhance efficiency and quality within organizational processes.
- Quality Tools and Leadership Skills: You’ll have the opportunity to explore a diverse set of quality tools, honing your problem-solving capabilities for effective decision-making. Simultaneously, you’ll work on enhancing your leadership skills, equipping you to lead teams collaboratively and guide projects toward success.Get exposed to DMAIC problem-solving approach.
- Application and Career Advancement: In this section, you’ll apply your knowledge to real-world projects, earning a globally recognized Six Sigma Green Belt certification. This certification enhances your career prospects and empowers you to foster a culture of continuous improvement in your workplace.
Course Content
- Module 1
- Module 2
- Module 3
- Module 4
- Module 5
- Module 6
- Module 7
Introduction
- Quality Definition
- What is Quality
- Type of Quality Measure
- Continuously based approaches
- Certification based approaches
- History of Quality
- Continuous Improvement
- KAIZEN Methodology
- Element of KAIZEN
- KAIZEN Blitz
- KAIZEN cycle
- PDCA/ PDSA & Quality Tools
- Overview of Six Sigma
- History of Six Sigma
- Six Sigma reduces COPQ
- Six Sigma- Transformational Approach
- Six Sigma benefits for companies
- Annual Saving of Black Belt Study
- Six Sigma Revolution & follower companies
- What is Six Sigma?
- Six Sigma thinking
- Process
- Six Sigma as a set of tools
- Metric
- Six Sigma metrics with CP, % &
Define Phase
- About Project
- Characteristics of a good project
- Project success Rule
- Source/idea to commence a Project
- VOC (Voice of Customer)
- VOB/VOP
- COPQ (Cost of poor Quality)
- VOIC ( Voice of Internal Customer)
- RTY ( Rolled Throughput yield)
- RTY Calculation with Example
- OTD ( On-Time-Delivery)
- FTR (First Time Yield/Right)
- R R (Return Rate)
- NPR (Number of problem Report
- Tools to Identify Projects.
- COPIS
- Project Selection Approaches
- Top-down approach
- Bottom-up approach
Define Phase (Project Start)
- Project Charter
- Business Case
- Problem and Goal Statement
- Project Scope and Boundaries
- Project Team
- Project Timelines
- Communication Plan
- Project Charter in Six Sigma Project
- Expected Benefit from Project
- Forming Team
- Potential Pitfalls
- Cost Benefit Analysis
- Project Go/ No-go
- Process mapping
- Types of Process Map
- Flow Chart
- SIPOC/COPIS
- Definition
- Process Map Standard Notations
- Benefits of process mapping
- Components of Process
- Failure Modes and Effects Analysis (FMEA)
- Design FMEA
- Process FMEA
- Risk Management System
Measure Phase
- Define Performance Standard
- Operational definition
- Target, Specification limit, and Defect
- Defect, Unit, Opportunity
- Defect per unit
- Defect per million opportunity
- Discrete/ Continuous data
- Measurement System Analysis
- Accuracy / Bias
- Repeatability
- Reproducibility
- Stability
- Understanding Precision and Accuracy
- Equipment Variation
- Appraiser Variation & Attribute Gage standards
- Benchmark of Repeatability, Reproducibility,
- Accuracy
- Gage (ANOVA)
- Benchmark of 3 Rules in Gage R&R
- Data Collection Plan
- Sampling
- Convenience sampling
- Systematic sampling
- Judgmental sam
- Brainstorming of possible reason
- Control Impact Matrix
- Data Collection Planning
- Random Sampling
- Stratified Random Sampling
- Baseline Process
Analyze Phase
- 8 Wastes
- Over-production
- Excess Inventory
- Unnecessary Processing
- Unnecessary Motion
- Defects
- Waiting
- Transportation & Conveyance
- Unutilized Skills [New]
- 5 S and Visual Management
- SORT (Seiri)
- Set in Order (Seiton)
- Shine(Seiso)
- Standardize (Seiketsu)
- Sustain (Shitsuke)
Improve Phase
- Screening of Vital X’s
- Cost & Impact Matrix
- Solution Identification through QFD & Brainstorming
- Risk Analysis
- Pilot Solution —Proof of concept
- Improvement validation through 2 sample T-tests, 2 Variance or visualization tools (Graphical summary, Box Plot, etc.)
- Full implementation of Solution
- Validation of improvement again Goal Statement (Hypothesis Testing, 1 sample T-Test, 1 Variance, or 1 Wilcoxon or 1 Sample Sign Test)
- MSA (Measurement System Analysis)
Control Phase
- Special Cause variation ( 8 Rules to see Special Cause in Chart)
- Common Cause Variation
- Control Charts in Minitab
- Continuous Y
- Individual Chart
- Moving Range chart
- I-MR Chart
- X bar Chart
- R Chart
- S Chart
- X-R Chart
- X-S Chart
- Discrete Y (project)
- Minitab practice
- C- Chart
- IJ Chart
- NP Chart
- P Chart
- Producer Risk
- Consumer Risk
- Risk Management & Analysis
- Poka-yoke (Mistake Proofing Activity)
- Prevention
- Detection
- Cost-benefit Analysis for Project Submission
- Develop Control Plan
- Project closure
- Tollgate Review
- Possible Roadblocks in the organization for delaying the project or not getting successful
- Operational Challenges
Institutional Benefits
HCGI Team
Our team at High Career Growth International is the backbone of our success. Comprising passionate experts like Rajesh Rajan, Asma Gazala, Ravi Raj, K Padma Sirisha, and Badrul Ahmed, we bring a wealth of knowledge and experience to our training programs, ensuring that our students receive the very best in education and guidance.
Globally Recognized
HCGI is globally recognized for its excellence in providing career-enhancing education and training. Our certifications hold international acclaim, empowering individuals worldwide to achieve their professional goals.
Career guidance and Counseling
Embark on your Lean Six Sigma Green Belt journey with HCGI. Our certified program is your second step in this methodology, globally recognized for providing a deep understanding of process improvement. With the guidance of a Lean Six Sigma Black Belt professional, you’ll not only learn the tools and methods but also grasp the “why” behind Lean Six Sigma. Boost your career and make a real impact with us.
Why Prefer HCGI
- Diverse Courses: HCG provides diverse Six Sigma courses for all levels Yellow Belt, Green Belt, Black Belt, and a comprehensive Masters Program. They also offer additional technical and management courses, including ISO 9001-2015, IATF 16949-2016, and Lean Manufacturing Training.
- Global Recognition: HCG’s training methods are globally recognized, establishing them as a leader in Six Sigma Training worldwide.
- Real-World Exposure: HCG offers real-world exposure with free Six Sigma Live Projects, preparing students for industry challenges and ensuring practical skills.
- Additional Benefits: Complementary courses such as Lean Management and ISO 9001:2015 certification are part of the package, ensuring that students gain an edge in the competitive job market.
- Job Assistance and Placement: HCG offers 100% job assistance with high salary packages (10-24 LPA), prioritizing your career success.
Key Benefits
Pursuing a Six Sigma Green Belt at HCGI comes with several valuable benefits.
- High-Quality Training: HCGI is known for its excellence in education and training. You’ll receive top-notch instruction and resources.
- Global Recognition: HCGI’s certification is highly respected worldwide, enhancing your career prospects on a global scale.
- In-Depth Knowledge: Gain a thorough understanding of Lean Six Sigma tools and methodologies, equipping you to drive process improvements effectively.
- Problem-Solving Skills: Develop strong analytical and problem-solving skills that are highly valued by employers across industries.
- Practical Application: Learn not only the ‘how’ but also the ‘why’ of Lean Six Sigma, enabling you to apply your knowledge to real-world challenges.
- Guidance from Experts: Benefit from the mentorship of experienced Lean Six Sigma Black Belt professionals who will help you excel in your journey.
- Career Advancement: Enhance your resume with a globally recognized certification, opening doors to higher-level positions and increased earning potential.
- Contribution to Excellence: Become a catalyst for continuous improvement in your organization, making a significant impact on efficiency and quality.
Eligibility
Eligibility criteria for pursuing Six Sigma Green Belt at HCGI
- Educational Background: Typically, there are no strict educational requirements for Green Belt certification. Candidates with a high school diploma or equivalent can often enroll.
- Work Experience: While not always mandatory, having some work experience, especially in a process-oriented role, can be beneficial and is sometimes recommended.
- Basic Knowledge: A foundational understanding of business processes and a willingness to learn and participate in process improvement projects are often sufficient.
- Prerequisite Certifications: Some institutions or organizations may require candidates to have completed the Six Sigma Yellow Belt certification before pursuing the Green Belt.
See What Our Students Say
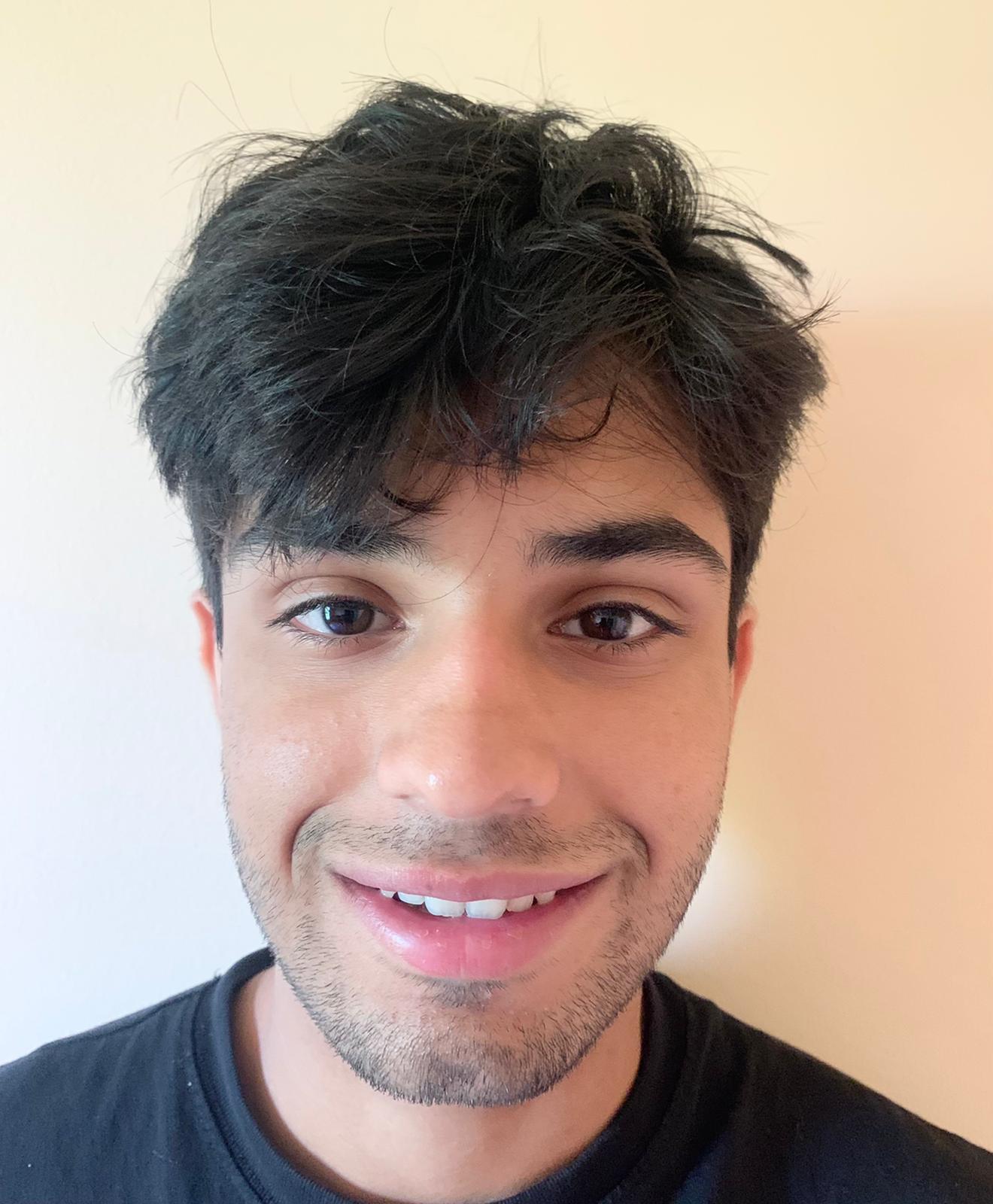
“As I am going into my freshman year of college, I took both Lean Six Sigma Yellow & Green Belt to give me a strong understanding of Quality Control and the detail layout of how many businesses operate. By taking this course, and through all the help of my professor Rajesh, I have developed such a strong passion for Six Sigma!….”
Prajeet Tripathy
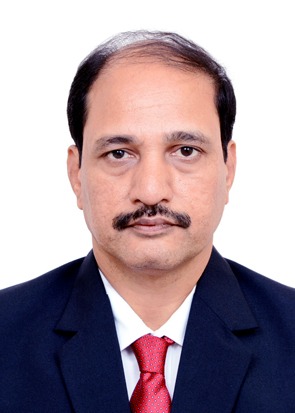
“Mn srinivasa. Dy manager working in machine manufacturing in efd induction Pvt limited .best six Sigma training in Bangalore I suggest for my friends also to this institute.very supportive team thank you HCG team”
Srinivas Nayanappa
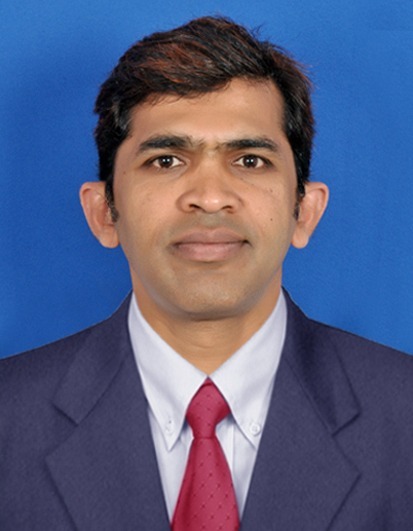
“Lean Six Sigma and Lean Manager Course deliverables from Mr.Rajesh Ranjan is Worthwhile. Initially felt how he may take up without manufacturing back ground, but the right way of choosing examples and the way of patience of adoption is a true value for the time and the career. I wish him to Excel his Best for ever…”
Seetha Rama Rao T.V.
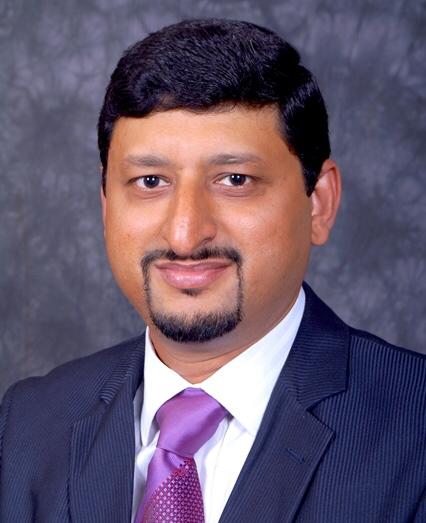
It started as classroom training and with COVID related challenges, the center adapted to going online and that too very effectively. The thing that I found most beneficial was the openness of the coach Mr. Rajesh Ranjan to approach him with any doubts…”
Jayesh Dudpuri
Lets Start the Journey of Knowledge
01. Enroll
- Click on the icon below
- Fill the details
- Upload a soft copy of passport size photo (for certification)
- Make investment
02. Payment
UPI
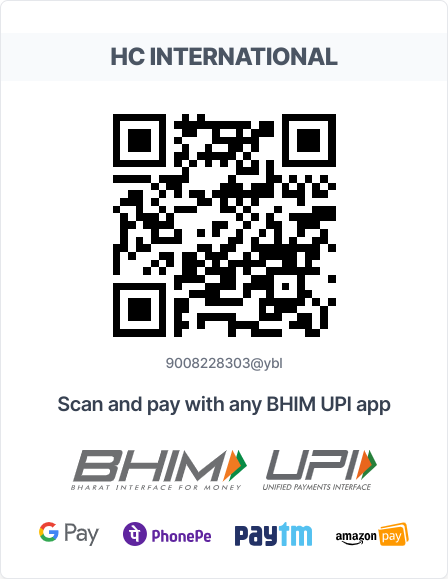
Account Transfer
- Account Number: 50200059747842
- IFSC Code: HDFC0000140
- Bank Name: HDFC
- Account Holder: HIGH CAREER GROWTH PVT LTD
- Branch: R.T Nagar
03. Attend the Course
- WhatsApp group will be created for each batch and all communication regarding the sessions will be informed here.
- Trainer will share the joining/meeting link on the day of session along side the study material (updated ones) Trainer will also share the session videos at the end of each sessions.
- Try the daily test for better understanding of concepts Complete the assignments for hands on experience of using some of the tools.
04. Certificate
- Complete the exam with a min of 85% and get certified in each belts (CLSSYB, CLSSGB, CLSSBB & Certified Lean Manager).
- Classroom
- Online
Classroom training
- 5 Days
- Course duration 48hrs – 60hrs
- MiniTab practicals
- Weekdays & Weekends
- 24 x 7 Support
- Flexibile timings
Online training
- 5 Days
- Course duration 48hrs – 60hrs
- MiniTab practicals
- Weekdays & Weekends
- 24 x 7 Support
- Flexibile timings